Technology | 07.04.2025
10 Tips to Avoid Collisions on 5-Axis CNC Machines
By: Hebert Garza
07.04.2025
Share
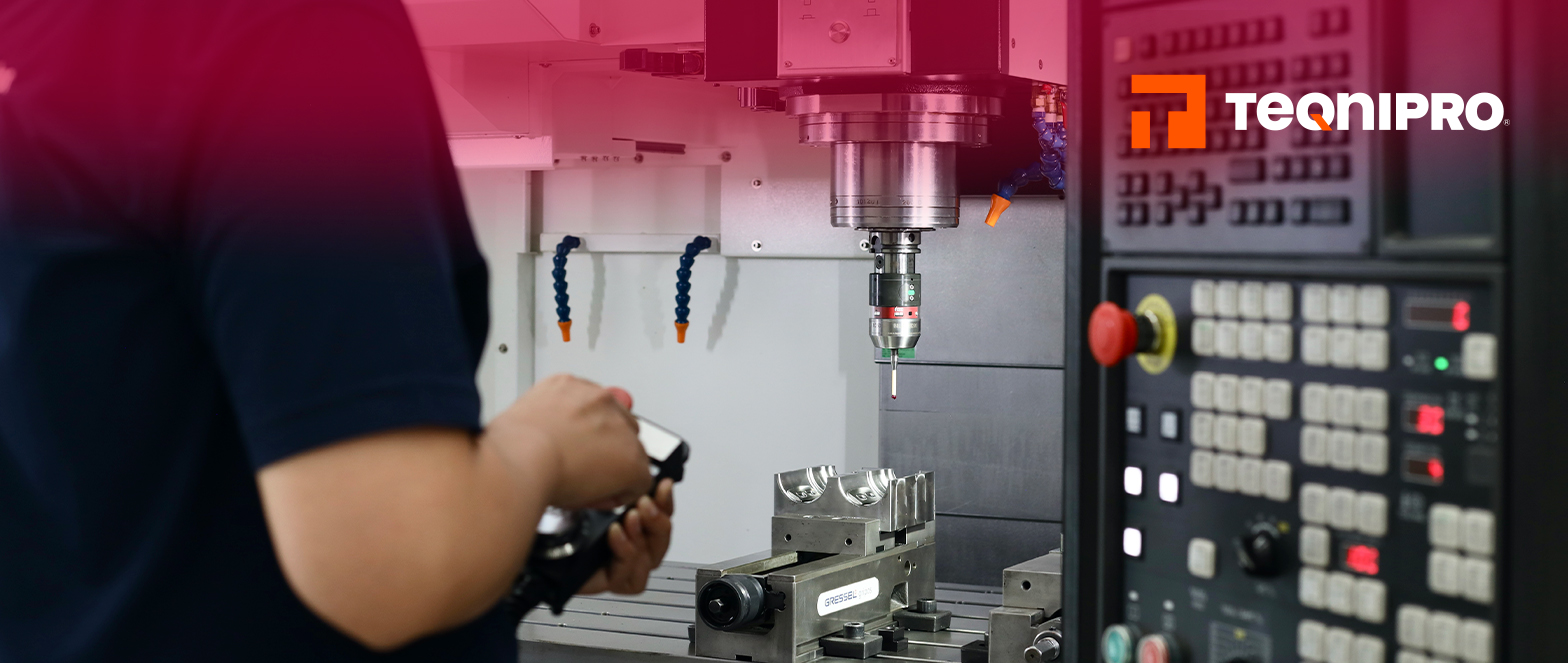
5-axis machining has revolutionized manufacturing, enabling complex geometries to be machined into high-precision parts. However, it also presents significant challenges, especially in preventing collisions between tools, parts and CNC machine components. Here are the best tips for minimizing the risk of collisions in 5-axis machining center programming.
1. Confirm Machine Calibration
Every 5-axis CNC machine has a unique calibration or kinematic configuration. It is crucial to know whether the system is table-table, spindle-spindle or table-spindle type, as this affects how the axes move and possible interferences.
2. Use advanced CAM software
High-quality CAM software allows you to program efficient toolpaths and anticipate collisions. In the case of Okuma, this brand has a system called Collision Avoidance System, a function that stops the operation immediately before the collision in both manual and automatic operations; this allows the operator to concentrate on machining without additional worries and reduces setup times for the first cycle times.
3. Perform simulations prior to production
Okuma’s Digital Twin simulation system facilitates testing in a virtual environment complete with 3D models. This highly accurate simulation calculates cycle times, geometries and energy consumption. In addition, it helps to calculate production schedules with estimated cycle times, as well as estimated production times and costs.
4. Define precision and motion stability
Okuma’s SERVONavi function improves accuracy during machining, as well as surface quality of the cut, optimizing accuracy and results in both surface quality of machining. This option can also eliminate motion peaks, noise, vibration and fold marks resulting from long-term use of CNC machinery.
Also, setting rotational and linear axis limits in the CNC machine control software will prevent unexpected movements that can cause collisions.
5. Optimize cutting tool selection
Using tools that are too long or unsuitable for the CNC machine can increase the risk of collision with the workpiece or other machine components. It is recommended to select tools with the right length and the correct angle for the work to be performed.
6. Check the workpiece clamping
Poor clamping can cause the workpiece to move during machining, resulting in impacts with the tool or spindle. Make sure that the part is properly clamped and that the fixture does not interfere with the tool path.
7. Use proper roughing and finishing processes.
The use of well-planned roughing processes reduces unnecessary movements that can cause collisions. Roughing should be performed with safe strategies, minimizing abrupt changes of direction.
8. Establish safety and verification processes
Implementing checklists before running programs on the CNC machine is excellent practice. Checking the toolpath, part fixture and tooling before starting the machining cycle can prevent costly errors.
9. Programming and operation training
Operator knowledge is key to avoiding collisions. Providing ongoing training in the use of CAM software, CNC machine control and safety best practices reduces the risk of human error.
10. Real-time monitoring and the use of collision sensors.
Some modern machines have real-time monitoring systems and sensors that can detect potential collisions and stop the process before damage occurs. Integrating these technologies can save repair costs and downtime.
Preventing collisions on 5-axis machining centers is a task that requires a comprehensive approach, from proper CAM software selection to training personnel and implementing safety controls. Applying these tips will allow you to improve the efficiency of your processes and reduce tool and machine damage costs. Safety and planning are key to successful machining!